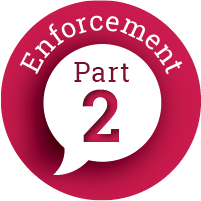
The Hospital Inspections team explains “Compliance with hygiene rules is important: after all, people’s lives depend on it”
Anyone who goes to hospital in Switzerland trusts that strict hygiene standards are applied to medical devices. But as they say, while trust is good, control is better: that’s why Swissmedic regularly carries out hospital inspections. Too often, the team comes upon serious shortcomings. An insight into the work of the inspector team.
Scalpel or scissors, endoscope or surgical robot: just four of the many medical devices that are used in Swiss hospitals. How are they cleaned, disinfected, sterilised, stored and maintained? Are hospitals aware of their responsibility – and do they meet the legal requirements? Monitoring this is part of Swissmedic’s legal mandate.
An annual report that makes headlines
In May of this year, the Medical Devices Operations and Hospitals Division, headed by Janine Conde, published a report on the inspections of 35 hospitals it carried out in 2021 and 2022. This received a lot of interest in the media, with comments such as “horrific” and “unsatisfactory.” Are conditions in our hospitals really so bad? “I don’t take any notice of sensational headlines”, says Janine Conde. “But the results of our inspections are indeed sobering. Hardly a single one of the inspected hospitals meets the legal requirements for sterilisation and maintenance – and that’s worrying. There’s a great need for improvement and investment in technical quality management, in the infrastructure of the reprocessing departments, and the basic and further training of their staff.”
Swissmedic inspects small private clinics as well as cantonal, regional, central and university hospitals. They are selected according to a multi-step scientific process. Whistleblower reports are also taken into account. The inspections focus on medical device maintenance, reprocessing and vigilance, and on the associated quality management system (QMS) required by law.
Teamwork as a factor for success
Swissmedic usually announces the inspection two to four weeks beforehand and asks to see documents concerning quality management and processes. This allows suspected weak points to be identified in advance. When visiting the hospital, the team of inspectors works in pairs to assess infrastructure and hygiene in the medical device reprocessing units (MDRUs) and the medical technology departments. The maintenance and vigilance IT system is checked, and a number of individual devices also undergo random checking. To assess staff qualification, Swissmedic examines job descriptions, training plans and evidence of training.
“In this highly varied work, a team combining diverse talents is a key factor in success”, says Janine Conde. Thus the five members of her Division have extremely different professional backgrounds – in chemistry, biology and microtechnology – as well as a command of a very wide range of languages. “But what’s most important is that they all communicate with one another continuously, align requirements and learn more about the job every day.”
Greater device safety saves money for the healthcare system
In the 2021 and 2022 inspections, Swissmedic found that there was often a lack of well-directed, effective quality management with appropriate action. In the MDRUs and the endoscopy departments, there were shortcomings in terms of staff qualification. Also, the premises often did not meet the hygiene requirements. In maintenance, poorly set responsibilities with external service providers gave grounds for criticism. In the vigilance area, staff have far too little awareness of the need to report serious events concerning medical devices.
“These observed deviations have an impact on the safety of the medical devices and thereby on the safety of patients”, says Janine Conde. “Compliance with hygiene rules is not being ‘finicky’, it’s important: human lives depend on it.”
So it was essential that hospitals introduce continuous improvement measures for medical device maintenance, reprocessing and vigilance – even if these involved making investments. “If the right action means fewer infections and follow-up treatments, hospitals save money for the healthcare system in the long term – and reduce patient suffering and unacceptable risks.”
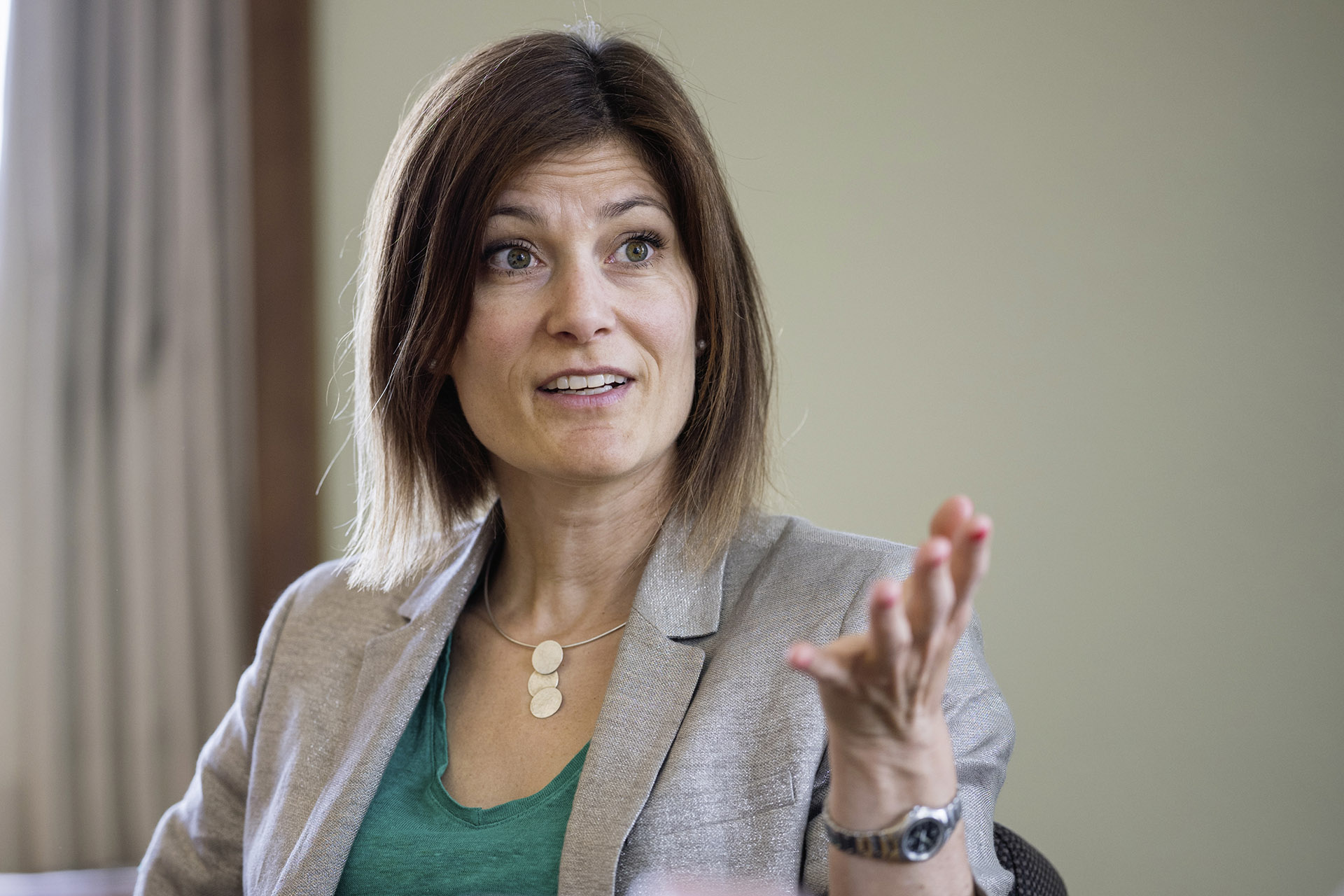
Sveva Crivelli, inspector, microtechnologist
“I like quickly and objectively assessing the complexity, the overall situation in a hospital. But above all, I value the friendly, constructive, inspiring and varied exchange with people from the widest range of professions. Despite the pressure that the hospital staff may feel before our visit, we generally get very positive feedback at the end of the inspection day.”
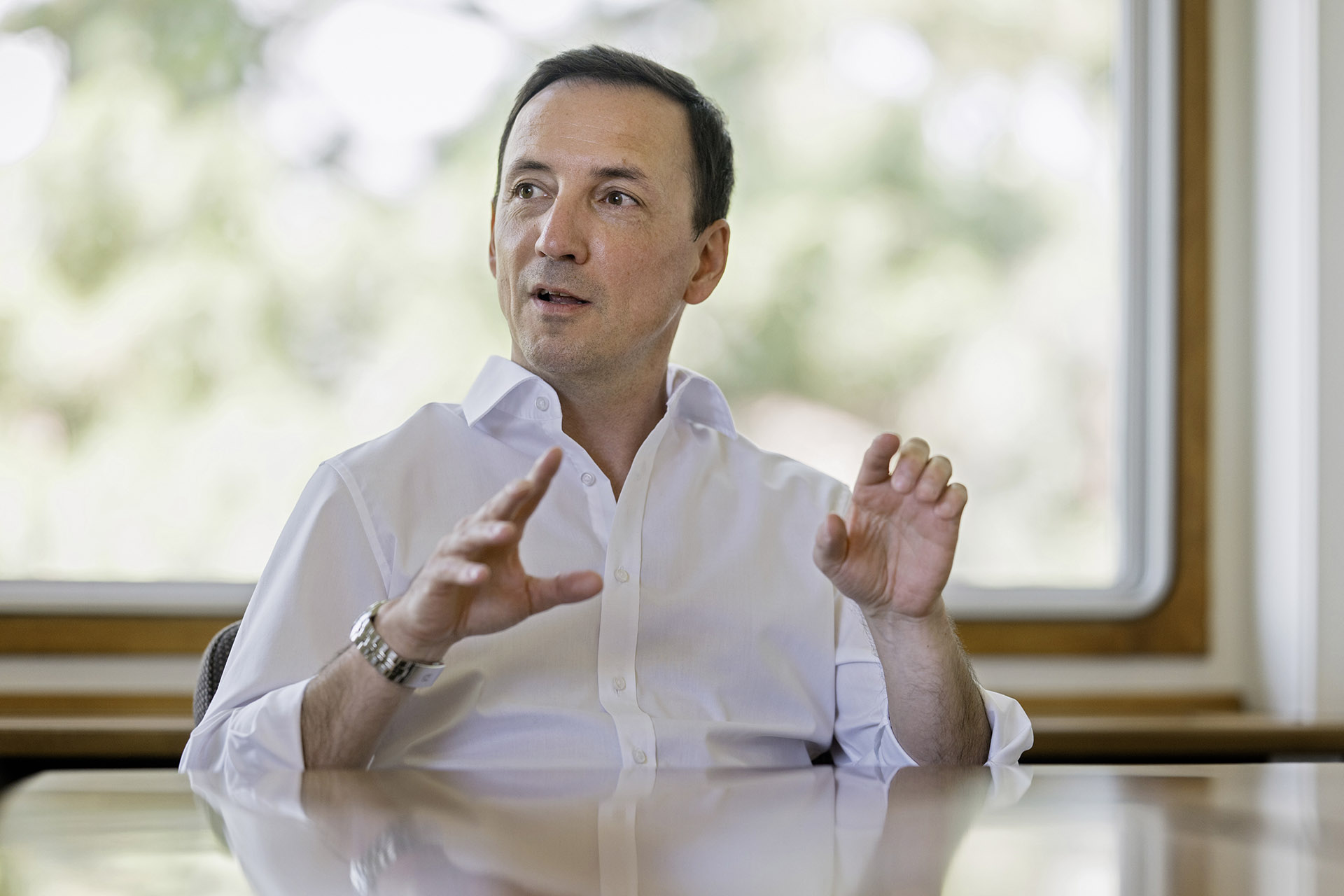
Rafael Moreno, senior inspector, biologist
“When I joined Swissmedic in 2015, hospital inspections regarding medical devices were still in the development stage and were undertaken as a secondary responsibility. We were rather derided as outliers, as at the time Swissmedic’s focus was on medicinal products. When I look back on the sometimes turbulent and challenging past eight years, I’m proud of what has been achieved and thankful that today hospital inspections have acquired the visibility, significance and status appropriate to them, both within and outside Swissmedic.”
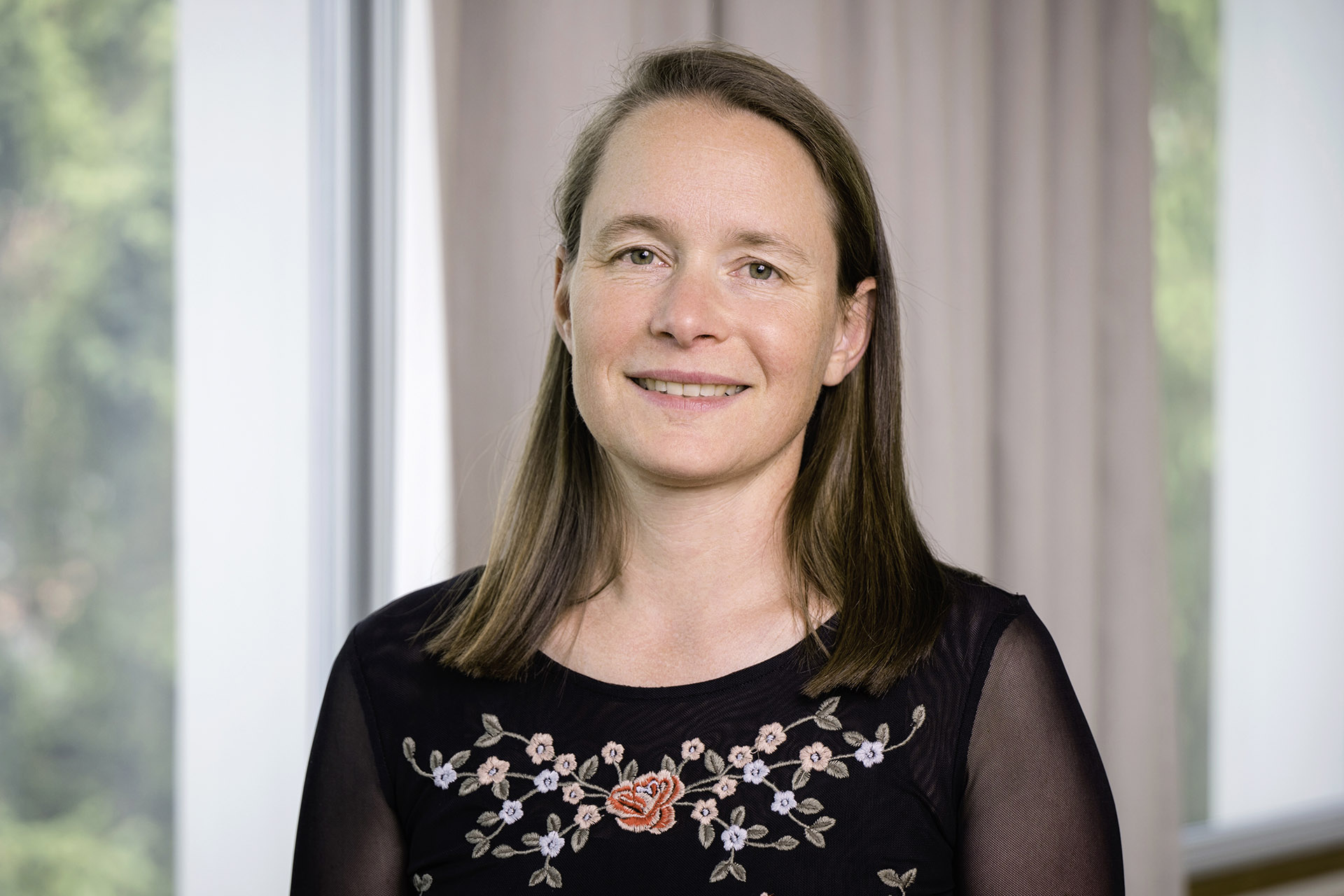
Frédérique Scherrer, inspector, chemical engineer
“We all have different backgrounds and experience, and the team is the sum of these! Some are most familiar with how medical devices or medicinal products are manufactured and placed on the market, others have experience of everyday work in hospitals, in clinical studies or the certification of reprocessing departments. This leads to deep and stimulating discussions on inspection-related topics. Each of us learns from these – and hospitals also benefit from them.”
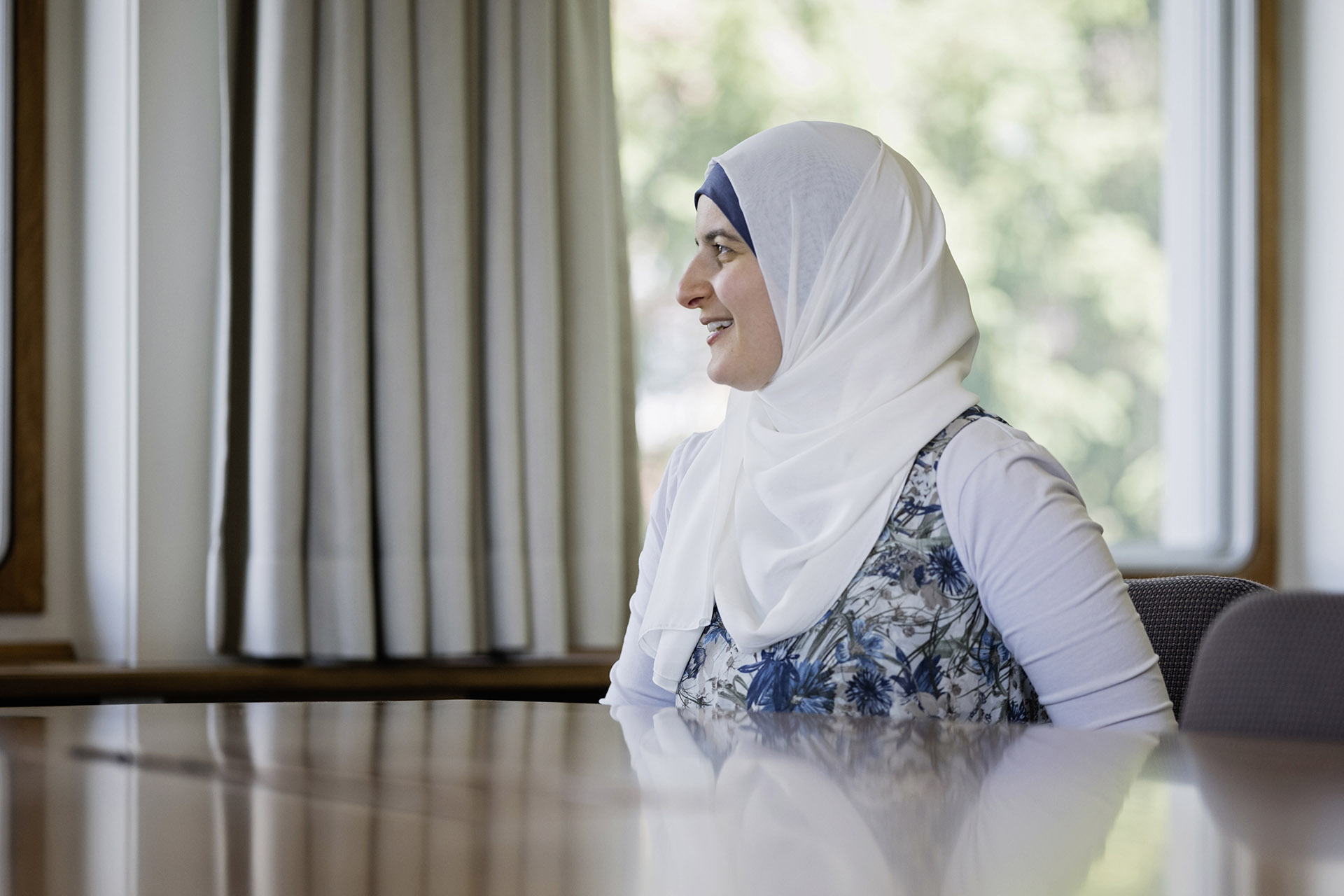
Ayah Khubieh, scientific assistant, life scientist
“I find a lot of meaning in my work. Our job is important and difficult, as we have to ensure the hospitals meet the statutory requirements. We help hospitals comply with the regulations and produce supporting documentation. I value our inspection team’s friendly approach and the fact that everyone is very committed to continually improving our inspections.”